“Absolutely top-notch!” says Lars Lundegaard about the quality of data collected at DanMAX. Lars is a Research Scientist at Haldor Topsoe, one of the big companies providing solutions supporting decarbonization and the green energy transition. During the five-day experiment, Lars and his colleagues teamed up with scientists from the University of Oslo to study the chemical structure of catalysts through X-Ray diffraction at the DanMAX beamline at MAX IV.
Haldor Topsoe is a trailblazer when it comes to scientific innovation. Considering that the company’s founder, Haldor Topsoe, after whom the company was named, was a scientist himself, it’s no surprise that the organisation is science-driven. Thus, this winter, the company has become the first industrial user at DanMAX, a newly launched beamline at MAX IV.
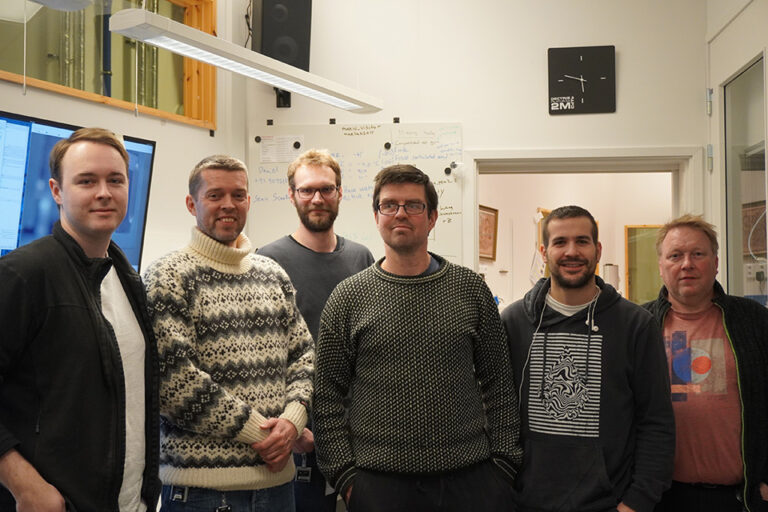
Together with a group of researchers from the University of Oslo, the company’s research team is conducting operando studies of the changes in the structure of catalysts during deactivation. In the study, different types of porous zeolites are used as samples. The scientists expose them to methanol which reacts inside the channels of the porous zeolite forming larger organic molecules. Some of the larger product molecules block the channels inside the zeolite, resulting in deactivation. At DanMAX, the scientists closely observe the structural changes occurring during deactivation and regeneration. This helps them understand the underlying mechanism and to prepare a better catalyst.
David Wragg, Senior Engineer from the University of Oslo, lists some of the benefits this study can bring to the industry: “First of all, it is important for sustainability. We can create more environmentally friendly catalysts that don’t need to be replaced as often by learning how to keep catalysts active longer. By doing this we can make the production more cost-efficient with less energy consumption.”
High time-resolution at MAX IV
“Conducting an operando study is difficult as you need to follow both structural and catalytic activity data to find a correlation between the two. In this case, we are using the diffraction technique to get structural information from various parts of the sample, with high time resolution, which is only possible at high-quality synchrotron beamlines.”, says Lars Lundegaard.
Lundegaard further mentions the value that MAX IV adds to this research: “During our user time, we only had a few technical problems, which is remarkable since it is commissioning beam time and our first visit. The beamline performance was great and generally stable, and the MAX IV staff was always there to support us… We will definitely be applying for more beam time and hope to be back soon.”
Are you also interested in doing industrial research at MAX IV? Don’t hesitate to contact our Industrial Relations Office. Feel free to be inspired by what other industrial companies have researched – have a look at our cases.