Modern-time manufacturing creates new challenges to tackle. So does additive manufacturing which is foreseen as the future of sustainable and cost-efficient production.
Additive manufacturing (AM), known by many as 3D printing, has already been adopted by various industries around the world and many have already succeeded in using this technique. There are advantages to such a production like fabrication of net-shaped structures, minimal waste generation, shorter production time, and cost-efficiency.
Taking into consideration these advantages, it is possible to predict that AM has irreplaceable importance for future production. Not surprisingly, Alfa Laval Technologies AB, a Swedish engineering company wants to explore the AM further. Collaborating with Swerim, a metal research institute they study the in-situ corrosion studies of AM stainless steel with the help of ambient pressure X-ray spectroscopy.
Studying corrosion features of AM steel
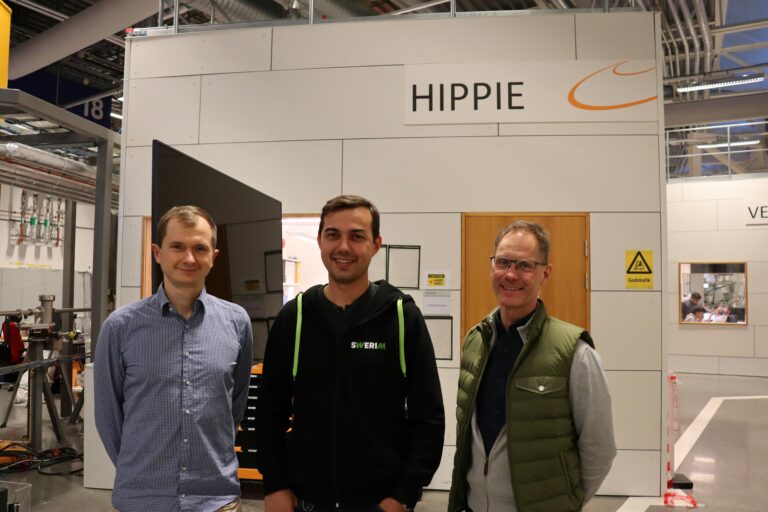
Daniel Klint, Material Specialist at Alfa Laval mentions the nature of the experiment saying, “This research is a spinoff from two AM projects also supported by the innovation agency. In this experiment, we use the operando technique at MAX IV HIPPIE beamline to explore the in-situ corrosion properties of polished AM samples.”
Being printed from powder, AM stainless steels need further processing. Usually, this involves hot isostatic pressing (HIP) treatment to eliminate pores and defects. The study of AM in-situ with ambient pressure X-ray spectroscopy will provide in-depth information about the effect of the HIP on chemical reactions in the corrosive environment.
Future of additively manufactured stainless steel production
Konstantin Simonov, Synchrotron Radiation Spectroscopy Expert at Swerim highlights the importance of the ambient pressure X-ray spectroscopy method to study the chemical reactions in the experiment: “If successfully implemented in this case, it will contribute to a better understanding of the effect of HIP treatment and subsequently, to more effective post-processing operations in AM stainless steel production with improved corrosion resistance.”
This study is sponsored by Vinnova, the Swedish innovation agency.
Are you also interested in doing industrial research at MAX IV? Don’t hesitate to contact our Industrial Relations Office. Feel free to be inspired by what other industrial companies have researched – have a look at our cases.