The future of efficient biofuel production is within reach. With measurements from MAX IV’s SPECIES beamline, a group from Lund University and RISE, Research Institutes of Sweden, has successfully developed a model catalyst that, once tuned, holds the potential to significantly improve the treatment process for the large-scale manufacture of viable biofuels from lignin. Lignin is a plant polymer only secondary in abundance to cellulose in nature.
Climate change and the rapid depletion of fossil fuel sources globally have injected new motivation into the pursuit of producing efficient, renewable feedstocks or biofuels for modern transportation. This shift is thanks in part to an industry-driven push for alternative energy sources through increased funding for research.
“There is a direct connection to the industry, and we use industrial catalysts [for investigations]. For example, I work in close collaboration with the company SunCarbon and the information we acquired is discussed with them. Our detailed understanding of the catalyst is, due to that, directly relevant to the industry,” said Sara Blomberg, principal investigator of the study, and postdoc in the Department of Chemical Engineering at Lund University.
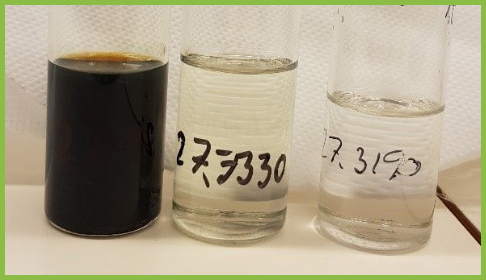
Catalysts are chemicals that promote reactions. Tackling the question, how can industrial catalysts efficiently transform lignin into high-quality fuels, requires a better understanding of the catalysts’ active site. Catalytic hydrotreatment processes, which remove oxygen and cleave the lignin macromolecules, drive this transformative reaction and are standardly used in the petrochemical industry. Industrial catalysts are infamously difficult to study at the atomic level due to the non-well-ordered state of particles, and the high surface-to-volume ratio of active metals that results when, as necessary, the catalyst is dispersed over oxide support.
Simplified models are often used to gain detailed knowledge about the catalytic process, such as the interaction between reactants and the active site of catalysts. However, these model catalysts can be an insufficient fit due to dissimilarities from the industrial sample. To create more relevant models, a more complete understanding of the properties of the industrial catalyst is necessary.
Modelling a catalyst
The Lund researchers created nanoparticles of nickel-molybdenum (NiMo) with a metallic core and a native oxide shell using a spark discharge method, a technique both flexible in what material can be tested, and known to produce very clean, size-selected particles. To understand their relevance as model catalysts in the hydrotreating process of lignin, the nanoparticles were compared to an industrial bimetallic NiMo catalyst (NiMo/δ-Al₂O₃) with surface and bulk measurements. The techniques used were X-ray photoelectron spectroscopy (XPS), scanning electron microscopy (SEM), transmission electron microscopy (TEM), and power X-ray diffraction (XRD) among others. The study is part of ongoing work to characterize lignin through the Lignin Research Project at Lund University.
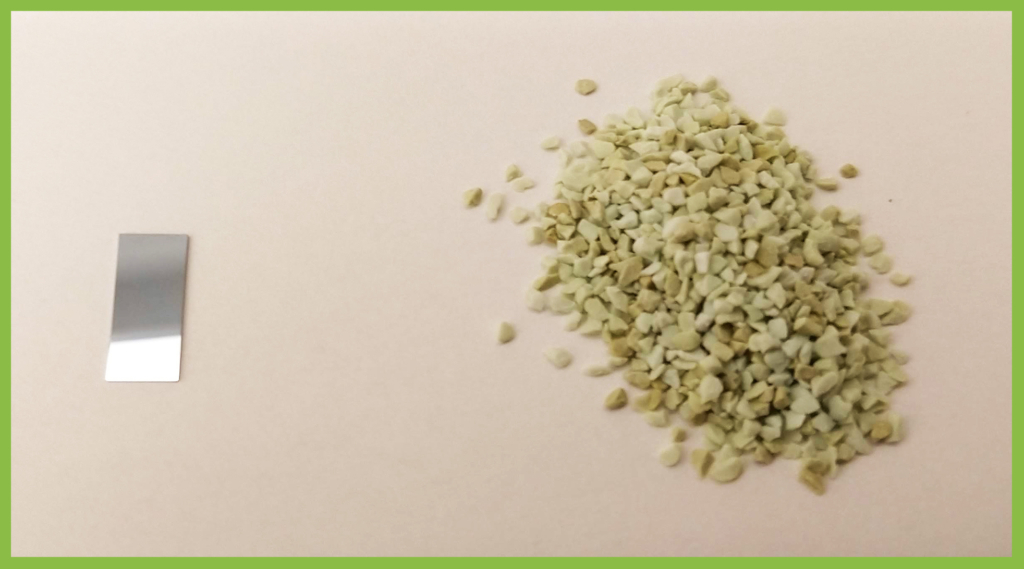
The XPS measurements, taken at SPECIES beamline using an X-ray anode source, enabled characterization of the model and industrial catalyst and shed light on similar properties between the two. Scientists also learned more about the active site of the industrial catalysts as they could clearly observe promotion in the reduction of molybdenum oxide with interactions of elements Ni and Mo during the reaction’s active phase.
As one of the scientific groups to use SPECIES before commissioning, solving unexpected challenges naturally, too, became part of the work, such as adjusting the conditions of the sample gas environment.
“In this case, the industrial catalyst contained aluminum oxide, which made the sample partially an insulator. Insulating surfaces are generally a problem for XPS, however, we were able to conduct the XPS measurement by conducting the experiment in ambient pressures, which was a new technique for us. After trying only pure argon gas, we successfully used air to create the ambient conditions, which due to ionisation by the X-rays, acts as the source of charge compensation,” said Esko Kokkonen, postdoc and beamline scientist who assisted in the work together with postdoc Niclas Johansson. “This type of charge compensation is only possible in places where one can measure at ambient conditions, with an ambient pressure XPS beamline such as SPECIES or the HIPPIE beamlines at MAX IV.”
These observations open a future path for researchers to tailor the model catalyst properties and design a model which more closely mirrors those of industrial catalysts.
“We can provide valuable information about the catalytic process that can be used in industry when they design and produce the catalysts for biofuel production to make the process even more efficient,” said Blomberg. “SunCarbon is already running a pilot plant for the production of lignin feed. Together with petrochemical catalytic hydrotreatment, it can produce biofuel and, within a short time frame, we should be able to fill up our cars with biofuel produced from lignin feedstock. The plan is to make the biofuel of such a production commercially available in a couple of years.”
Blomberg plans to continue to develop and improve the model catalyst system as well as perform more experiments in order to gain greater fundamental knowledge of the catalytic process taking place in the reactor in biofuel production. Experiments with model compound lignin at MAX IV’s Hippie beamline are scheduled for spring 2020.
Read their related work here.
Bimetallic Nanoparticles as a Model System for an Industrial NiMo Catalyst
Sara Blomberg, Niclas Johansson, Esko Kokkonen, Jenny Rissler, Linnéa Kollberg, Calle Preger, Sara M Franzén, Maria E Messing, Christian Hulteberg
. Materials 2019, 12(22), 3727; https://doi.org/10.3390/ma12223727
You might also like: